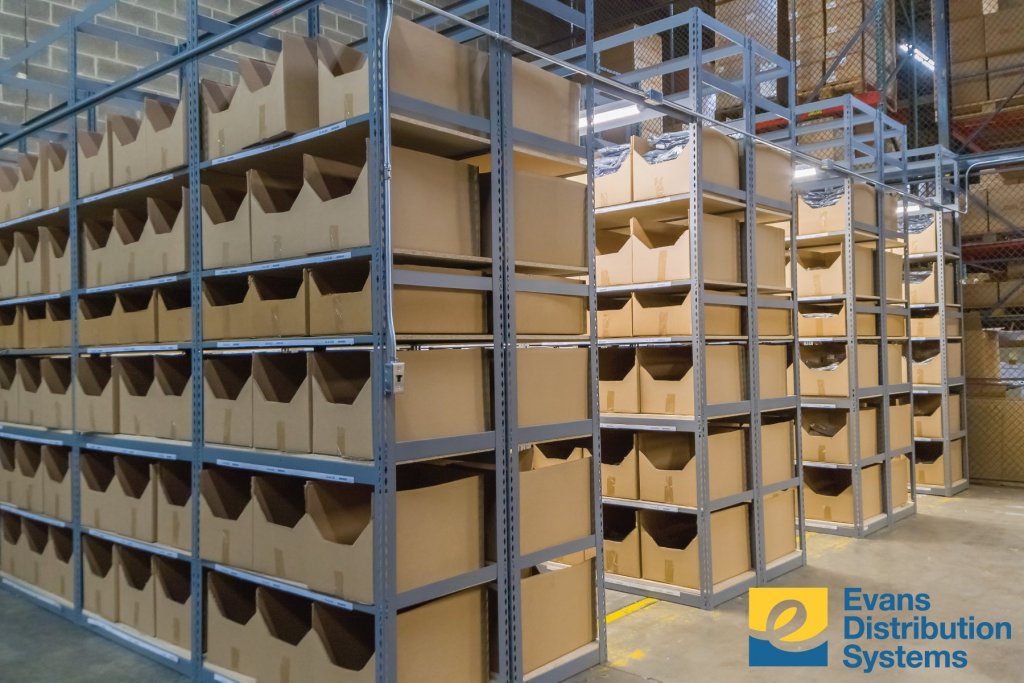
In a time where warehouses are at capacity, it’s wise to review your space utilization. This allows warehouses to make the most of their space and bring on more customers.
“Warehouse customers create a revolving door of products coming in and out,” says Rich Huziak, Sr. Operations Manager at Evans. “This is especially true when you’re taking on new customers. You always need to evaluate your design and layout. Does it still make sense? Do we need to move things around?”
Here are a few considerations:
- Congestion – It’s hard to operate in a congested area. Many times, goods are moved around to clear an area to make products more accessible. Multiple moves increase costs and slow down processing. Warehouses need a designated staging area by the docks to process inbound and outbound shipments.
- High turnover vs. low turnover – When a warehouse asks for an average turn rate or past shipment list, they are assessing how often a product goes in and out. This will dictate placement within the warehouse. High turn products need to be closer to the staging area or in high traffic areas. Products with a low turn should be stored in a less accessible area or high on a racking system.
- Aisle width – Wider aisles are more accessible than narrow aisles. This will increase speed and efficiency in locating the products and assembling the shipments. On the other hand, narrow aisles increase storage capacity.
- FIFO & LIFO – Another important element to maximize space is understanding if the product is first-in-first-out (FIFO) or last-in-first-out (LIFO). High density storage limits the accessibility of products. If the product is LIFO, low density storage is the better option.
- Reduce honeycombing – As products move in and out of the warehouse it generates empty space, known as honeycombing. Products need to be moved to fill that space and free up underutilized space. But products also need to be organized, either by SKU or turn so that they are easy to locate.
- Seasonality – Some businesses are highly seasonal. Warehouse layout should account for seasonality, including square footage, material handling associates and accessibility during peak season.
- Stacking requirements – Another important feature is a product’s stacking requirements. Customers need to specify if the product has no stacking, two-high, or three-high, which directly relates to the size and weight of the goods and the threshold for damage. Safety is another consideration; the higher a product is stacked the more risk of falling and injuring an associate.
- Racking & depth – Racking provides use of vertical space and can be very effective in space utilization. Some racking systems have double-depth racking. Products with low turn rates are ideal for double racking systems.
Inventory management data is a great place to start when considering space utilization. This will help you identify turn rates, inventory volume, seasonality and other important factors that go into your warehouse layout. It is advised to review this data on a quarterly basis, especially in times of tight capacity or an influx of new customers.