Evans Distribution Systems may be a 90-year-old 3PL company, but its warehouse technology is state-of-the-art. The company just invested in a machine vision system with artificial intelligence to optimize its warehouse packing line.
The ADLINK Edge™ Smart Pallet solution improves accuracy and efficiency using two GigE cameras, an Edge AI Gateway computer and ADLINK Edge™ software . The system uses machine vision to record and classify contents in packages as they move through the line as a quality check and uses rule-based analytics to identify inconsistencies to the packing list. Essentially, it’s an automated quality assessment system.
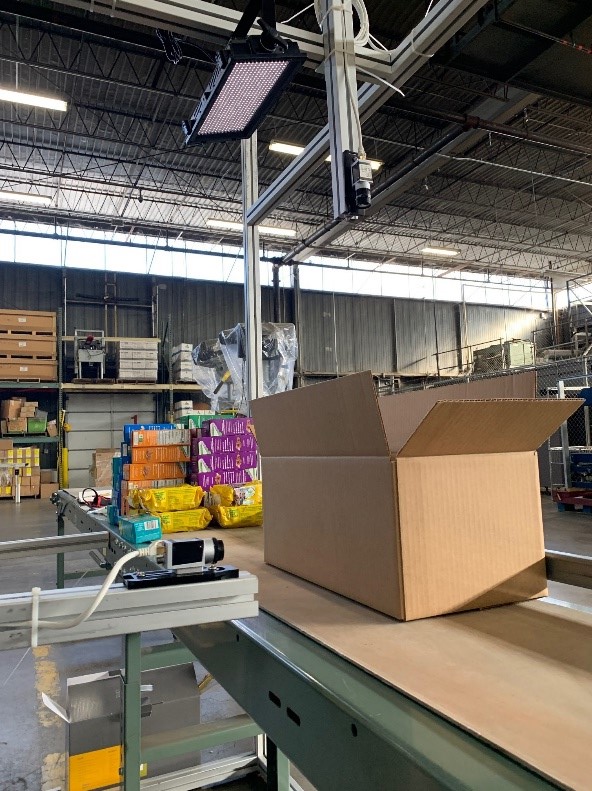
“One of the most skilled jobs on the line is the quality assurance technician. They need to quickly observe if the orders are packed correctly or incorrectly. This machine is over 99% accurate, allowing us to utilize those skills in other areas of the packing line,” says Steve Ruch, Vice President of Warehousing at Evans.
How It Works
How can a machine identify and understand the contents within a box? First, you have two cameras—one that peers down into the box contents and the other that reads a barcode, or unique identifier, containing the packing list. As the package moves through the quality check-point, two images are recorded and a classification model identifies the object. The model training system known as VMLINK, teaches the computer to identify objects in hundreds of different positions, lighting scenes, and other variances. The repetition of this modeling is critical to performance and accuracy. From there, the image pixels are converted into data and fed through a software system that is connected to Evans’ Warehouse Management System. The data is matched to the packing list and if the contents are inconsistent, a label is printed on the box to signal a packing error which can then be swiftly corrected.
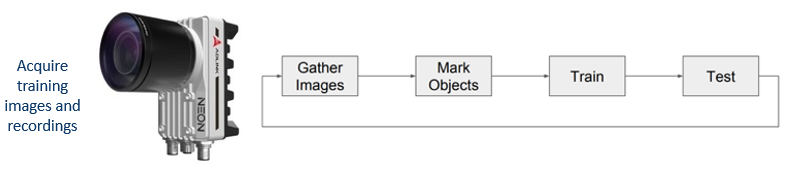
Long Term Impact of Automated Technology
The business case for a visual automation system is strong. “This is only the tip of the iceberg of potential uses and optimization of our operations,” Ruch says.
For one thing, the system can be trained to classify any object, including a different product, a person, or forklift. This means it could aid in facial recognition of employees, or it could be used as an inventory management system, where it can record the placement of goods within a warehouse. Or it can conduct traceability audits, where a digital event is created to denote what was last seen in a box, at what time and by whom.
There’s a lot of potential and growth in machine vision and artificial intelligence in a warehouse environment. “The goal is to enhance our current operations with a nondisruptive technology. The conveyor still works in the same way; only now we can allocate resources in a more efficient way on another part of the line,” Ruch says.
As Evans enters its first season using the new system, warehouse managers will be tracking KPIs closely to truly understand the return on investment. This investment is a small step toward a larger organizational goal: To provide the highest quality service to Evans customers using people and innovation to enhance the end-to-end supply chain.